Introduction
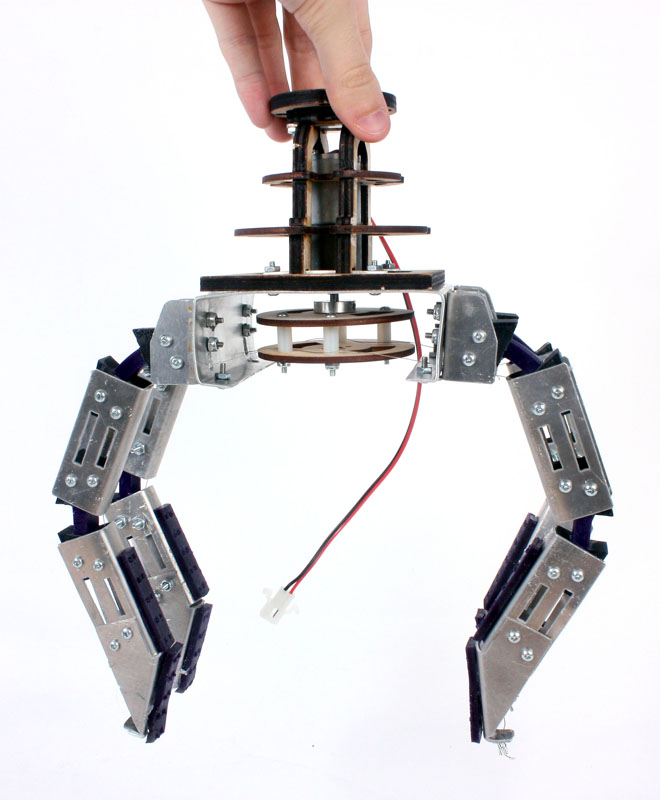
The challenge: Design and manufacture an underactuated mechanical hand
The materials available: 50-52 aluminum sheet metal, 1/4" and 1/8" baltic birch plywood, Vytaflex polymers, and a ABS rapid prototyping thermoplastic.
The competition categories: Grasping envelope ratio, grasped mass to hand mass ratio, dexterity, and aesthetic appeal.
Our design was developed with the intention of fulfilling the grasping requirements in an aesthetically creative manner. In doing so, the team made knowing sacrifices in the mass ratio criteria so that we could better appeal to the aesthetic challenge by modeling the prototype to resemble an octopus of four tentacles, or a quadrapus.
Design Overview
Our primary goal was to easily grasp spherical objects as well as participate in the other challenges. Our second objective was to create a unique design that had identity and character.
However, our design was limited by the availability of materials, unexpected manufacturing difficulties, and overall practicality. As such, our original six-fingered design was truncated to only four tentacles, and the stability of the joints was weakened. In the end we settled for a hand that strove to invoke an aquatic feel: a hand that moved and looked like an underwater creature. In that we succeeded.
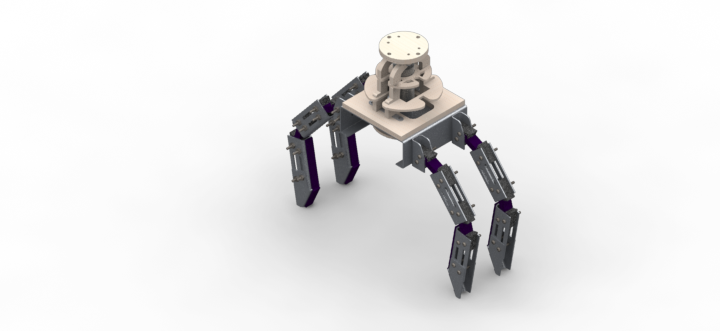
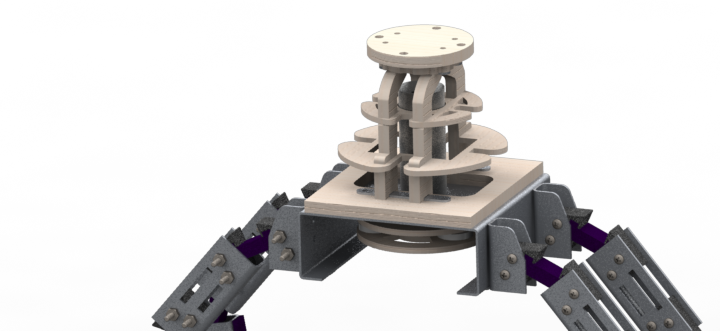
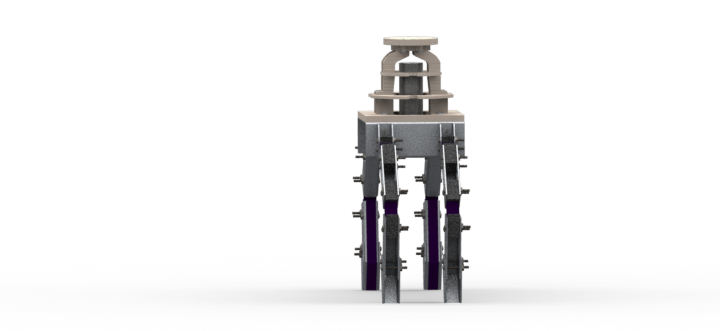

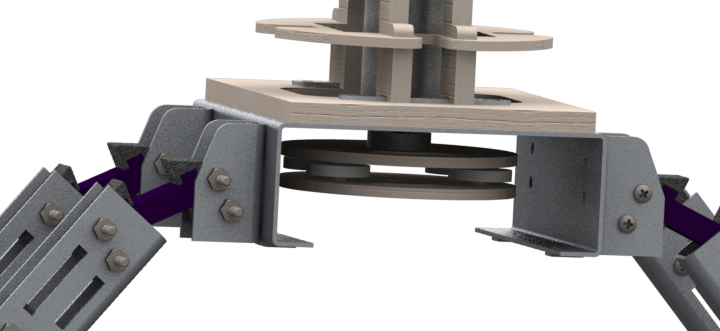
Design renders. Click to view higher resolution.
Structure
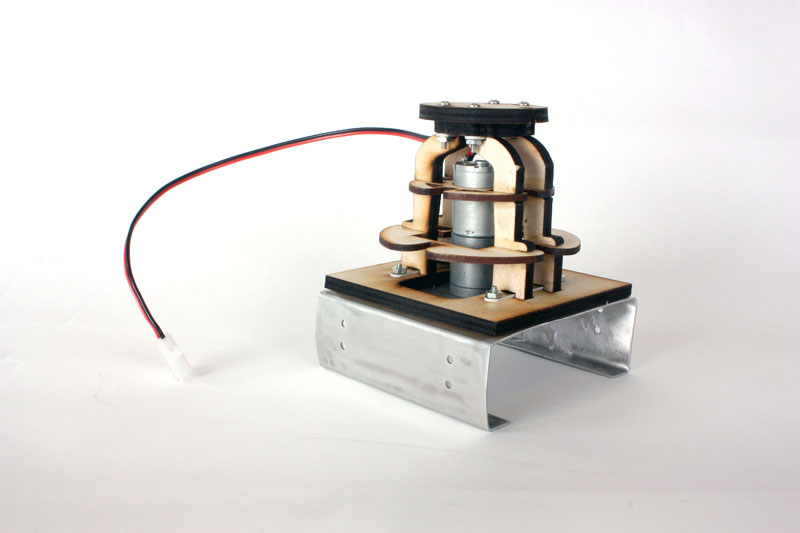
The main compnonents of the structure in our final design were the chassis, motor mount, and four tentacles.
The design of the base was simple. Utilizing a combination of 1/4" and 1/8" thick plywood, a strong interface was created between the arm mount and the hand. It needed to fit the four bolt mounts, while also support the much larger sheet metal transmission housing. An interlocking rib design was chosen in order to accomplish both of these requirements, while also minimzing material use and weight. Besides simply mounting the hand to the robotic arm, the base structure also needed to encapsulate the motor that will actuate the hand. The ribbed design was conducive to this and allowed for the hollow compartment to house the motor.
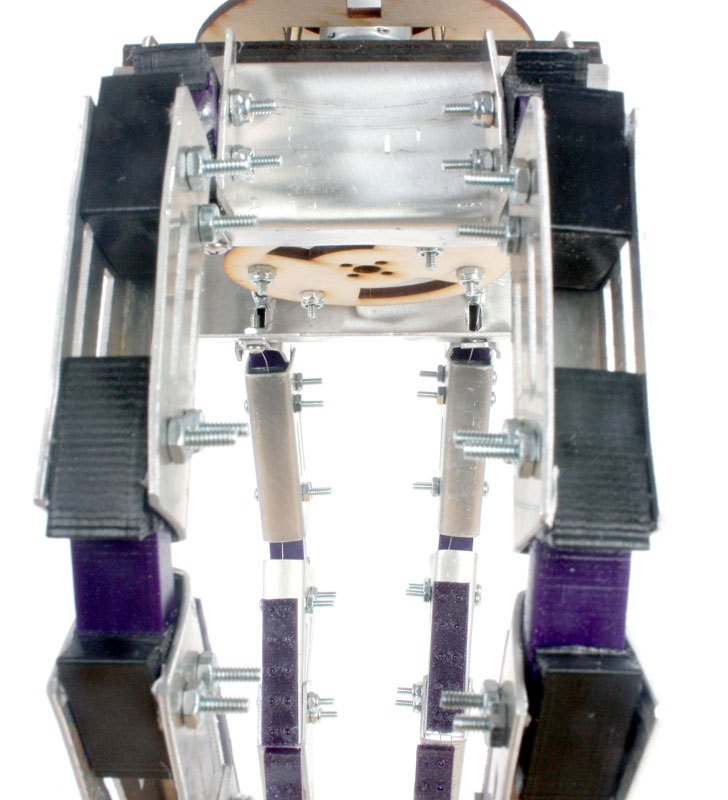
The strucutral housing of the transmission utlized the favorable bending characteristics of sheet metal to easily encase the transmission. The sheet metal bracket served three main functions. First, it was the primary mounting hardware for the motor. Two bolts screwed in through the sheet metal and into the motor mount. This ensured maximum transfer of torque from the motor to the transmission with minimal backlash. Secondly, the bracket protected the transmission. Life in the aquatic is dangerous and sometimes deadly. No self-respecting underwater creature would subject his most critical transfer of power to the rigors of nature without a protective shell. Thirdly, it provided the mounting points for the tentacles. The sheet metal proved strong enough for such a connection and was perfect for the task.
The structure of the tentacles was designed to mimic the tentacles of his natural counterparts. Consisting of two jointed segments, the sheet metal intended to connect the joints and present an inward face for the purposes of grasping an object. Two rectangular pieces mounted to the 3D printed jointed segments, while a third angled section provided a favorable angle for grasping at the fingertips. The bottom joint mounted to the transmission housing via a small, bent sheet metal bracket that was sufficient for securing the tentacles from the forces they would endure. A crucial aspect of our aquatic design was the integration of polymers that induced an underwater feel. We chose the Vytaflex 60 polymer for its hardness characteristics. The relatively weighty sheet metal components added much inertia to the moving tentacles. Under this weight, the unsupported and relatively thin polymers had much flex in the lateral direction. When assembled as a whole and mounted to the moving robotic arm, the loose tentacles looked as though they were in an underwater environment, moving lithely and yet subject to the whims of the currents and the will of angry Poseiden.
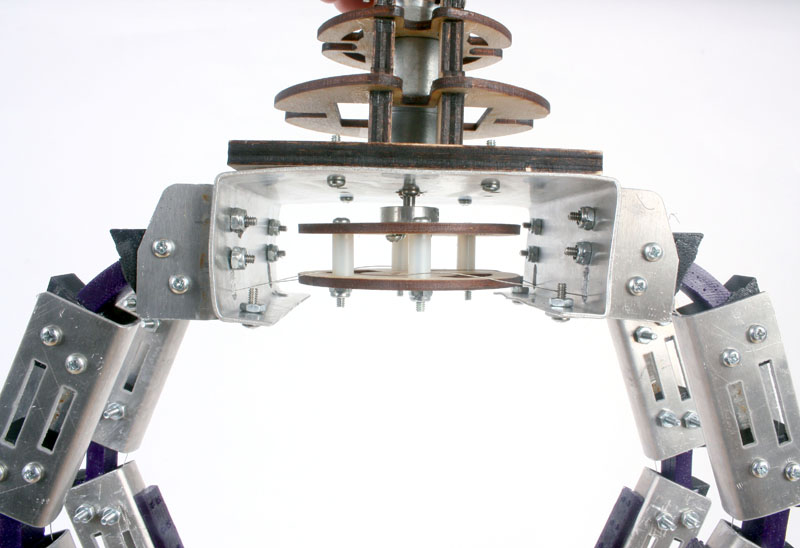
Transmission
Power is transmitted through an underactuated cable system. One cable is run through the entire length of two opposing fingers, thereby creating two couples. When the cable is under tension, the tenctacle is retracted. Between the fingers and in the middle of the chassis is a unique tranmssion system. Designed to be both simple, and therefore resistant to operational failure, and compact, it effectively accomplished both. Learning from previous iterations of the hand, we found that the traditional cable pulley system requires the pulleys to be free-floating, thereby occupying an inconvienent amount of space. An alternative design was chosen that stacked two horizontal setes of pulleys that accomplished the same task of underactuation. A rotating spindle driven by the motor winds the opposing wires simultaneously, while still allowing for the cable to slide horizontally in response to resistance from a finger. The second iteration utilized pulleys, while the final design replaced them with frictionless nylon spacer instead, eliminating the possibility of cable derailing. This system allows one of the fingers in a pair to continue grasping if the other is inhibited.
Power
The quadrapus is powered by a brushed DC motor. This direct current gearmotor has a metal gearbox with a ratio of 499:1, which requires low current and provides high torque at a low velocity. The high torque allows for a stronger grasp when picking up objects. A molex wire was soldered and connected to the pins of the motor to interface with the controller and power source.
The motor rests on the chassis and is secured by the plywood cutouts. The shaft fits through a hole in the main frame and is fastened with screws to the transmission system using a metal spindle.
The final transfer of power occurs at the interface between the tentacles and the object to be grasped. This was optimized by using the polymer Vytaflex 10 to provide a grippy surface with a high friction coefficient to aid in the grasping of objects. The miniature suction cups on the polymer also add to the underwater vibe.
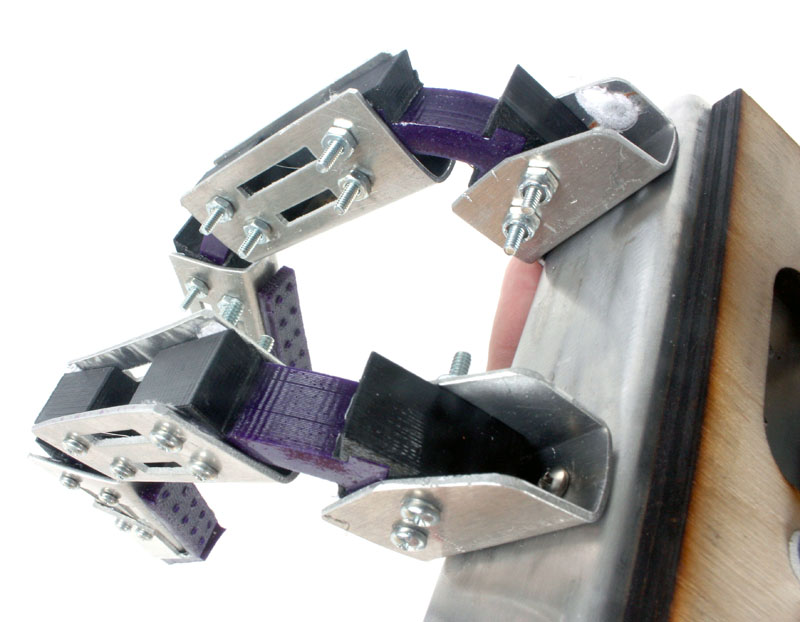
Fabrication
We made our hand using a combination of laser-cut plywood, waterjet sheet metal, and rapid prototyping ABS thermoplastic. One advantage of all these fabriacation methods is the inclusion of internal features. Features that would otherwise be much more involved to replicate using traditional manufacturing methods can easily be incorporated. For example, a sharp right angle cut can be included in the waterjet sheet metal. If one were to manually fabricate such a cut, not only would that require post-machining on a mill, but such a sharp cut could not be easily made using a round end-mill. Similar fine features were included in our plywood that would require a similar level of involvement in post-machining that was rendered unecessary due to the ease of a CAD-driven waterjet cutter. Accuracy of hole placement is also an added bonus and saved much assembly and post-machining time. The most radical fabrication paradigm lies in the 3D printing, however. While the other two materials are cut in two dimensions, the thermoplastic is additively fabricated to make any three dimensional shape. This is extremely useful for the creative use of polymers, as we incorporated for both our joints and grippy fingers.
The disadvantage of the sheet metal waterjet is the need to tree all parts in a chain to prevent small parts from falling in between the cracks of the grid. However, this is a minor trade-off when compared to the benefits. Rapid prototyping's greatest weakness is the weakness of the ABS. We circumvented this flaw by avoiding its use in the main structural components. Its resolution is also not extremely high, but it is sufficient for this application.
Future Improvements
If we could design another iteration of the hand, we would have firstly apllied more attention to the material constraints. Late awareness severely limited our design and curbed much of what we planned to have in our design. We intended to combine the strengths of linkages with the ease and flexibility of polymers to create stronger tentacles. Material constraints prevented this from happening. We also had trouble tuning the tension of our cables on the quadrapus. It is important that the two pairs of tentacles contract at the same rate in order to effectively grasp an object. In the future, instead of just using crimps we would have liked to have an adjustable tensioner. The cable could have been anchored to a bolt of adjustable position that could be adjusted to match its counterpart.