Introduction
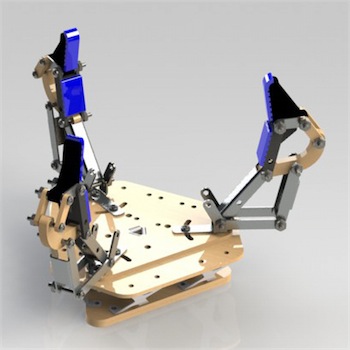
We were tasked with building a hand that can grasp as wide a range of things as possible. The goal was to produce as versatile a hand as possible - one that could pick up objects small and large, had a ration of hand weight to lifting weight, and could adapt to pick up oddly-shaped objects.
The hand had to be underactuated; this means that we were only allowed actuation in one dimension, and had to turn that into multidimensional adaptive motion. This greatly increases mechanical complexity, while greatly reducing controller complexity.
We were constrained to one 12x12 sheet of sheet metal, one 12x12 sheet of eighth inch plywood, one 12x12 sheet of quarter inch plywood, and 5 cubic inches of 3D-printed ABS plastic. This constraint created a need to find a way to effectively integrate these different materials, as we were not allowed enough of each material type to produce a hand purely out of one manufacturing method.
Design Overview
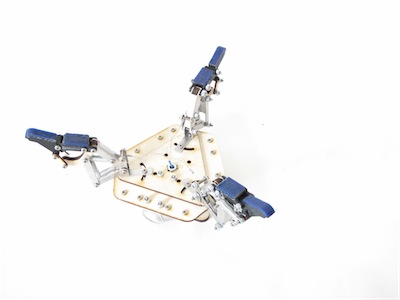
Throughout the project, our design was primarily driven by function — we aimed to make the most efficient, effective hands possible by adjusting our designs to fit our manufacturing materials.
Our initial hand was designed to be 3D printed in ABS plastic. Inspired by some other under-actuated hands that used polymer joints, we decided to create a tri-fingered hand that used springy polymers to link the phalanges and cables to contract the fingers around an object. A notable feature of this hand was that the fingers were placed on sprung pivots (visible in the top view) that allowed them to torque and adapt to grab differently shaped objects. We kept this design when we moved to the sheet metal and plywood hand, although we switched to a linkage finger design that utilizes mechanical leverage and springs to actuate the fingers in the place of polymers and cables.
For our final design, we kept most elements of our sheet metal and plywood design, but used a caged base rather than a single sheet of plywood. We also used the ABS plastic and polymer at our disposal to give grip to our phalanges while also reducing their weight. Since the auto-pivoting concept was implemented with only mild success in both prior iterations, we decided to maintain the ability to change the angle of the fingers; however, we designed them to be manually set rather than have them auto-pivot via springs.
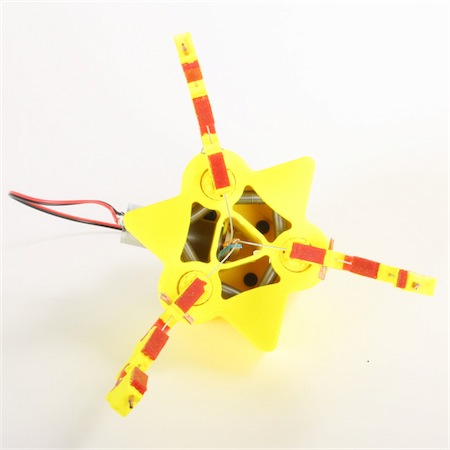
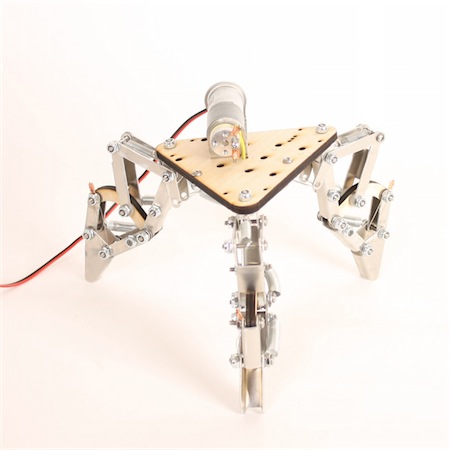
Structure
Our hand consists of three linkage fingers and a plywood base which housese the motor and can be attached to the robotic arm.
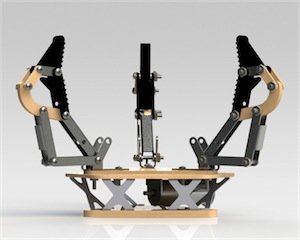
The base is constructed of two plywood triangles held together with x-shaped sheet metal brackets. The lower base piece has holes for mounting to the arm and is smaller so that it doesn’t interfere with the robotic arm while it is moving. The upper base is made of two layers of 1/8” plywood provides a place for the fingers and motor to mount to. The motor is mounted on a bent sheet metal bracket attached to the upper base piece. In the center of the base is a triangular hole with dowel pins embedded on the three edges. This is where the cable from the pulley attached to the motor routes up and to each of the fingers. Ideally, the dowel pins provide a nice smooth surface for the cable to run over so that it doesn’t get damaged in any way. However, in reality the cable got stuck in the gap between the plywood and the dowel pins, so we used a spare hex nut to keep the cable from running over the wood.
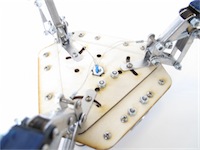
The upper base also contains 4 holes directly above the holes in the lower base which mount to the arm. These are big enough to get a hex key in and out for easy installation and removal of the hand.
Our fingers are attached to the base by an adjustable pivot mechanism, which rotates around a single bolt at the center of the finger. The angle of the finger is fixed by a bolt that is tightened into place through an arc cut into the top of our base. The angle of the fingers is adjustable to allow for different grasps, to grab differently shaped objects.
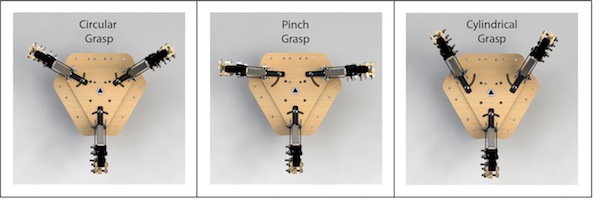
Our linkage fingers were based off of the three DOF underactuated finger presented by Laliberte, Birglen and Gosselin. The lengths of each of the linkages in the finger were determined by the formulas presented in their paper. We only had to choose the lengths of the pieces which would be interfacing with the object we would be picking up. To determine these lengths we decided on an overall length which seemed reasonable and then used ratios between the phalanges that were similar to that of a human finger.
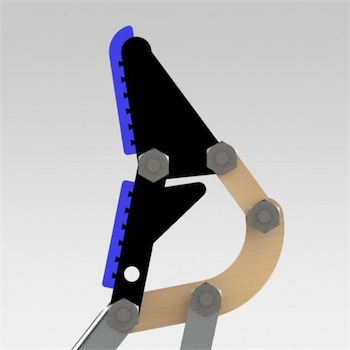
The top two phalanges are made of printed ABS and have molded polymer pads for added grip. A rib at the back of the middle phalange serves as a mechanical stop so that the finger doesn’t bend back away from the object it is picking up. The bottom phalanx is made of bent sheet metal because we determined that it was not important for it to have better grip, it’s role is mainly for support. In general we constructed linkages that needed more support out of bent sheet metal.
Transmission
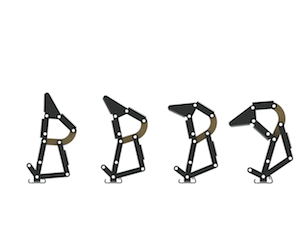
Our linkage finger design features cables tracking from the lever arms at the base of each finger to the center of the hand “palm,” where they are wrapped together and around a pulley on the motor shaft. When the motor turns, the pulley creates tension in the cables and causes the fingers to contract. If one or more phalanges encounter an obstruction, the remaining phalanges continue to close on account of our linkage design; the power is transmitted via the lever arm (the sheet metal component closest to the base) up and around the back of the linkages, in such a way that the load is distributed equally among the fingers. The figure keyframes illustrate a finger contracting thusly.
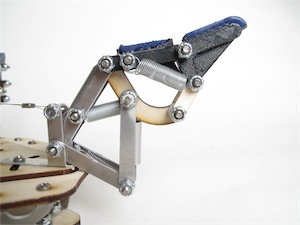
Power
We powered our hand with a high-torque brushed DC motor that winds the wires from each finger through the center of the base board, simultaneously pulling all three fingers into a closed grip. The motor has a 499:1 gearbox attached to its output shaft. This incredibly high gear reduction is optimal for our hand's functionality, as we don’t care about the speed of the reactions of our hand, but rather its grasping power. We will not be attempting to grab anything that moves, and therefore closing speed is not a relevant characteristic to consider when choosing a motor; strength of grasp is a far more relevant factor. The motor is operated manually instead of using position feedback control, since we lack a potentiometer. This allows us to turn the motor indefinitely in either direction, rather than being limited to a 330-degree range, and thus we can rotate the pulley enough to fully actuate the fingers.
Fabrication
Fabrication of the components of our hand was quick. Our sheet metal parts, including several of the finger joints and the brackets between the top and bottom base piece, were cut from a sheet of 0.05 inch 5052 Aluminum stock using a water jet cutter. Our plywood parts, including our base pieces and some small joints on each finger, were cut from 1/4 and 1/8 inch sheets of Baltic birch plywood using a laser cutter. Our plastic parts, the two outermost phalanges on each finger, were created from ABS plastic stock using a 3D printer. Finally, to create the rubber components of our hand - the grips on the edges of the fingers - we poured Vytaflex 10 urethane rubber into a mold, then filed down the mold when the rubber dried.
The assembly of our hand was designed to be streamlined; having learned from our previous iterations, we took measures to overcome the assembly challenges we faced. Grinding and bending the sheet metal parts took the better part of three hours, and assembling and attaching the fingers and bases took no more than two hours total. This gives us a total assembly time of around five hours, not counting the time it took the Vytaflex polymer to dry. The majority of our screws were M4 Phillips, and we mainly used lock nuts since ordinary nuts had a tendency to unscrew on their own.
Our design also allowed for error; at one point the motor we were using broke and had to be replaced, but due to clever design, we were not required to take any part of the hand apart. We simply unscrewed it from the bracket and slid a new one into place. We also kept ease of access in mind - we added holes in the top part of the base which allowed us to very easily screw in the attachments to the robotic arm. The only significant revision we made was replacing the three dowels in the center of the hand with a single 1/4 inch nut; the tendons were getting stuck in the corners of the triangle, and we decided that a round opening would be much safer and less likely to kink the steel cables.
Future Improvements
Perhaps our hand's greatest weakness is its inability to grasp small or oddly-shaped objects; during trials, we tried and failed to pick up a pencil, a key, and a wet bar of soap. The problem of picking up cylindrical or differently-shaped objects could potentially be solved by increasing the range of rotation for each of the fingers, allowing two of the fingers to close parallel and opposite the third, or any number of other finger configurations.
In addition, because the fingers do not close inward at the same rate (that is to say, they never come together exactly), the fingers often fail to pick up objects that are very close the the table surface (such as a key, flat on the table). This could be remedied by calibrating the fingers carefully, possibly wiring each finger to the motor separately in order to calibrate on the fly.
The problem with the wet bar of soap is lack of friction; attempting to pick it up from the sides proved futile. The soap could be picked up, however, if there were curvature at the end of each finger - just enough to be able to lift the soap off the table and constrict it.
Finally, our hand tended not to open itself all the way if the fingers were pointed downward (gravity pulled down on the fingers, counteracting the springs pulling them away from the center of the hand). This could be fixed by using stronger springs in the fingers - it would require more torque from the motor, but would allow the hand to grip large objects (a basketball, for instance) far more easily.